If you know the right jewelry making techniques, anything is possible in jewelry design. From lost wax casting and glass fusing to bead weaving and clay jewelry, jewelers use a wide array of techniques to bring their visions to life. Below, the experts at MKM Jewelry break down some of the most common jewelry making processes.
Lost Wax Casting
3D Printing
In this jewelry making techniques the casting process can translate the most minute details into metal, and hard wax is ideal for sculpting intricate models. As technology advances, some designers are opting to design their jewelry with CAD software and 3D print their models in casting wax. This can result in intricate designs that are near perfect due to the precision of computer design software.The Vacuum Chamber
Once the wax model is complete, a metal cylinder, referred to as a flask, is attached to the base of the mold, surrounding the wax model. A fine grain plaster is mixed for the investment mold, and the mixture is placed in a vacuum chamber to remove any air bubbles. If a vacuum chamber is not available, the mixture can be left to rest for 10 to 20 minutes for similar results. The plaster mixture is poured into the flask, covering the wax mold. The filled flask is again put into a vacuum chamber to remove any newly formed air bubbles. In the casting process, air bubbles will become tiny metal welts on the final piece, so removing them early on in the process is critical in creating a flawless final product. Once the investment mold is completely dry, it is cleaned and placed inside a kiln. The kiln is run at 1300 degrees Fahrenheit for up to twelve hours, until the mold has completely hardened. The extreme heat melts the original wax model, leaving a cavity inside of the investment mold that’s ready for metal.Using a Centrifuge
After the loss wax mold has cooled, it is time to cast it in metal. While it is possible to simply pour molten metal into the mold, metal smiths could use a jewelry making technique known as a centrifuge. A centrifuge is a mechanical device that spins incredibly quickly around one axis. The centrifuge creates the best results in casting because the centrifugal force pushes the liquidized metal into the deepest crevices of the mold. The mold is secured to one end of the centrifuge, and a small vessel with a funnel is attached to a hole. The casting metal, is heated until liquefied. Once the metal is molten, the centrifuge is wound several times and released. The spring mechanism causes the centrifuge to spin rapidly, forcing the liquefied metal into the mold. After the metal has been forced into the mold and has hardened, the piece can be cooled further and extracted for finishing.Beading
Stringing
The most basic beading technique is stringing. In stringing, beads are simply lined up along a string or cord. Patterns can be made by alternating bead shapes, sizes and colors.Bead Embroidery
Another jewelry making technique for making beaded jewelry is bead embroidery. With beaded embroidery, individual beads are stitched onto fabric or leather to make detailed patterns or images. Bead embroidery is an embellishment to a pre existing surface; it does not contribute to the structural integrity of the fabric. The fabric can be cut into irregular shapes to give the jewelry a unique form. Typically, bead embroidery is used on clothing and decorative objects, although the technique can also be used to adorn accessories, like belts, hats, leather cuffs, and suede chokers.Bead Weaving
Beaded jewelry can also be fabricated with a jewelry making technique known as bead weaving. In bead weaving, seed beads are strung onto a weft thread, which is then passed through the warp threads of a bead loom. Secured between the two rows of threads, woven beads can be used to create entire beaded surfaces with complex color blocking and patterns. Some popular stitching techniques include the Peyote Stitch, Brick Stitch, Square Stitch, Right Angle Stitch, and Daisy Stitch.Metalworking
Annealing
Annealing is a heating process that changes the physical, and sometimes chemical properties of metal to make it more workable. When a metalsmith anneals something, they heat the piece of metal with a torch until it is above the temperature of recrystallization, and then let it cool back down. When the metal has been recrystallized the molecular structure of the metal is altered, making it easier to manipulate.Hammering & Forging
After a piece has been annealed, it can be bent or hammered into shape. As the piece is worked, is becomes tougher and stronger. The jewelry making technique of manipulating metal with a hammer is known as forging. Metal is hammered into shape against an anvil, creating an attractive, dappled surface.Forming
Metal can take on a wide array of shapes through forming, which is when a piece of annealed metal is hammered against a hard, shaped surface. Through forming, flat sheets of metal can be transformed into curved and concave forms.Cutting & Drilling
Metalsmiths use a jeweler’s saw to cut shapes out of metal. The blade of a jewelry saw is very thin, with fine teeth. The blade of a jeweler’s saw is very fragile, and can snap easily, but their narrow silhouette gives metalworkers greater agility in their sawing, so they can cut out detailed shapes. The rough-cut edges of the metal are then filed and sanded until smooth.Joining
Metal can generally be joined through both hot and cold connections. While two metal pieces can be soldered or fused together with heat, they can also be joined through cold connections like screws or riveting.Finishing
As a piece nears completion, finishing steps like sanding, polishing, and buffing ensure the metal has a shiny, smooth surface. Finishing also ensures the piece is comfortable to wear — without any sharp edges or odd bumps. Finishes can be matte or shiny, and can be done by hand or with a machine.Clay Jewelry
Fused Glass
Experts to Help You Achieve Your Vision
Choosing the right jewelry making technique to bring your jewelry designs to life is crucial to creating a successful product. While some jewelry making techniques allow you to work from home on your own, others — like lost wax casting or metalworking — requires the training and knowledge of experts. If lost wax casting is your primary form of jewelry creation, reach out to MKM Jewelry today to discover how we can help you design and create high quality pieces.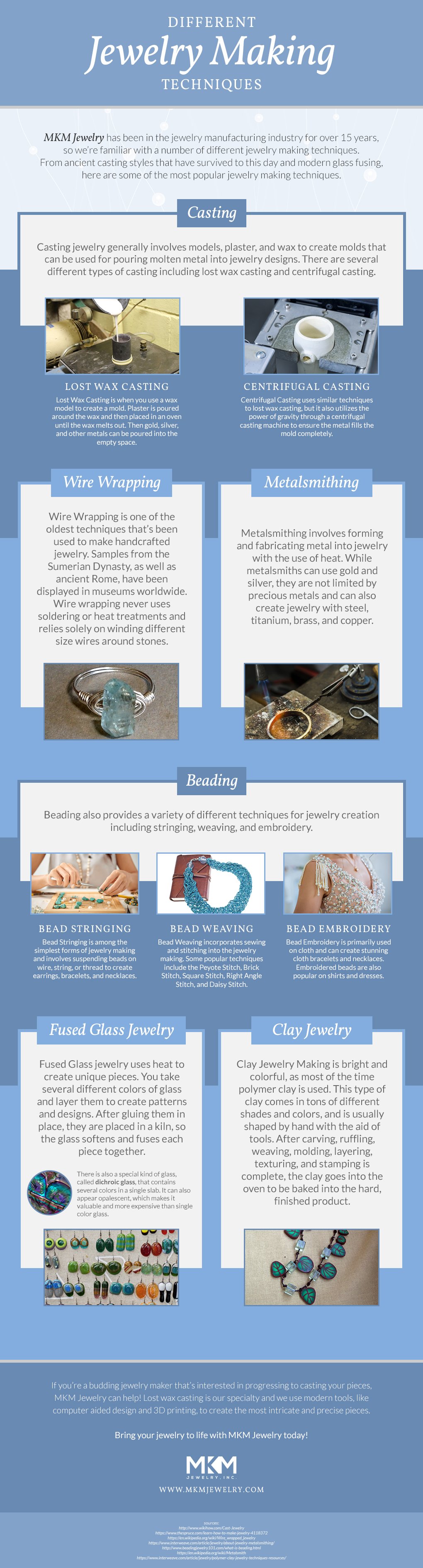
Leave a Comment